MasterSeries Blog
Optimisation of Steel Moment Connections
Steel connections are built up from several components from which the weakest one defines the capacity. There could be many connection configurations which are proper for our design situation, but how can we find the most economic one or which pass the design and/or the manufacturing requirements.
Modern design codes (e.g. Eurocode) use the Component method to evaluate typical steel connection connections. The Component method is an analytical procedure in which the connection is divided into individual components which are described in the codes (e.g. Chapter 6 of EN 1993-1-8).
Example Eurocode basic joint components | |||||
---|---|---|---|---|---|
Column web panel in shear | Column web in transverse compression | Column web in transverse tension | Column flange in bending | End-plate in bending | Etc. |
![]() |
![]() |
![]() |
![]() |
![]() |
Source: Eurocode EN1993-1-8
The overall resistance of the joint is determined based on the weakest tension and compression component’s resitance. Thus, finding the proper connection configuration is necessarily an iterative procedure:
- Calculating the tension resistance of the bolt rows, which involves the resistance of the bolts, end-plate, column flange etc.
- Calculating compression resistance (compressed column web and beam flange)
- Calculating the moment and shear resistance
When the resistance of the connection is evaluated, we can modify the weakest component (modifying the bolt rows pitch, adding stiffeners etc.) for greater resistance or greater economy, as appropriate and of course, the whole process is starting again.
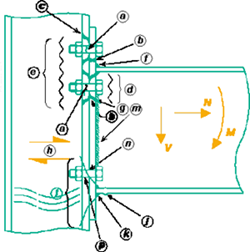
Source: SteelConstruction.info
Without an advanced connection design tool, connection optimisation is a very time-consuming task and sometimes the desired configuration can be only found by try and error.
In MasterSeries Connection Design, we have implemented some smart tools to enable you to create and design efficient steel connections:
- Default connection configuration
Built-in default connection configurations help you to have an engineered configuration right after creation. Most of the parameters (such as end-plate size, bolt rows’ position) are defined relative to the section size as a reference. Thus, during the optimisation process, the whole connection is adjusted accordingly
- Saving current connection configuration as default
If your project requires special connection configurations, you can save your current configuration as the default and all of the followers will be created based on it to accelerate the repetitive connection design
- Auto Design function
Auto Design function is a powerful and efficient tool which helps you find the most economical configuration in a second using the set boundaries. The Auto Design goes through the components in the same order as above, adjusting them until it finds the most economical solution which passes the requirements
- Multiple Loading Cases
No Connection is designed for only one loading case. Modern Engineering requires many loading combinations to be considered. With maximum forces not being coincident in ridgid frames all cases need to be checked. MasterSeries Connection Design checks these with ease
Explore how MasterSeries Connection Design can help you design more economical solutions and boost your productivity.
Try it for yourself with a free 14-day trial.
Categories
- About
- Beam Designer
- BIM
- Composite design
- Concrete Design
- Connections
- Dynamic
- Educational
- General
- LCA
- Masonry
- MasterFrame
- Pile Cap
- Portals
- PowerPad
- Retaining wall
- Steel Design
- Webinar
- Wind Analysis